Products
Echo 3D
Electro-Magnetic Field (EMF) Inspection Equipment.
ETher NDE is pleased to introduce ECHO-3D, the newest technology for the detection of surface breaking defects and crack depth measurements from Athena Industrial.
Echo-3D is ideal for inspection applications in petrochemical, oil & gas, power generation, aerospace, infrastructure and manufacturing industries and can be used for detecting surface and sub-surface defects in carbon steel, stainless steel, nickel alloys and aluminium; capable of identifying cracks and giving crack detection information in explosive clad carbon steel.
The Echo-3D software provides crack detection, crack depth information, 3D mapping and analysis.
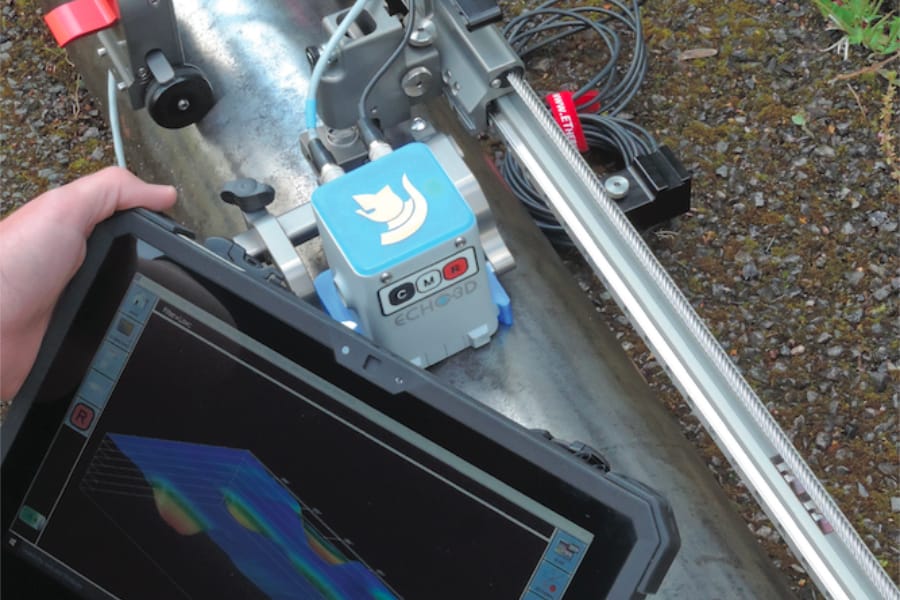
Echo-3D Principles of Operation
Echo-3D is an Electro-Magnetic Field (EMF) based technology that uses Electro-Magnetic Field Imaging (EMFI) to display surface breaking defects in a 3D image. A focussing element that creates a large hemi-elliptical toroidal field below the Sensor, creating EMF. The EMF shape is measured in the X, Y and Z planes by specially shaped antenna coils. Material permeability, conductivity, shape and distance from the surface to the sensor all affect the shape of the EMF. Echo-3D has the ability to cancel out these effects using a null command before scanning.
As the focused EMF from the Sensor passes over a surface breaking defect, such as a crack, SCC, or corrosion, the shape of the field is deformed. The degree and location of the field shift is measured and the translated into crack location, direction and depth. Additionally, the material is not left with a residual magnetic field and therefore does not require degaussing prior to return to service.
The Echo-3D can detect a defect through a coating because it does not require direct contact with the surface of the sample. This also eliminates the use of a couplant.
Presentation of Scan Data
Echo-3D has demonstrated its ability to detect surface breaking cracks in both ferrous and non-ferrous materials.
When the Sensor is used to scan a region via multiple passes, either by hand or by mechanical encoded scanner, the software stitches the adjacent B-Scans and produces a C-Scan image in real-time.
The data acquisition screen displays B-Scan and C-Scan images, which can be reviewed and analysed with the Echo-3D software after completion of the scan.
Once the scan is complete, selecting the C-Scan image instantly produces a 3D model, allowing the technician to rotate the image 360°.
Selecting the X-Y-Z icon, displays an analysis screen, which allows the technician to locate and mark defects, these defects are automatically included in the final report.
Advantages
- Require little of no surface preparation
- Inspects through paint, dirt and non-conductive coatings
- Surface contact not required
- Can be used with manual or automated scanners
- Detects and measures through >6mm coatings
- Inspects ferrous and non-ferrous materials
- Easy to learn icon based software
- One click PDF report writer
Features
Ideal applications
Surface Breaking Cracks, Surface Corrosion, Stress Corrosion Cracking (SCC)
Crack Detection
Cracks that are 19mm or longer. Can tolerate up to 15mm lift-off.
0 to 4.0 mm +/- 0.2mm or 10% (0.16” +/- 0.01”), whichever is greater
4.1mm to 5.5mm +/-0.5mm or 10% (0.16” to 0.22” +/-0.02”)
.
Reporting
Protected Document Format (PDF) reports are generated with the ECHO-3D software and include details of: Inspection Company; Client details; Technician details; Sensor set-up; and Project details with defect locations, depths, and optional site photographs and screen shots.
Standard Kit
Standard |
---|
DELL ruggedised touchscreen tablet |
ECHO-3D software |
Accessory Kit includes pipe shoes |
Tough Peli Case |
Gen II Echo-3D Sensor with encoder wheel & USB cable |
Check Plate |
Accessories
Please enquire for further information.